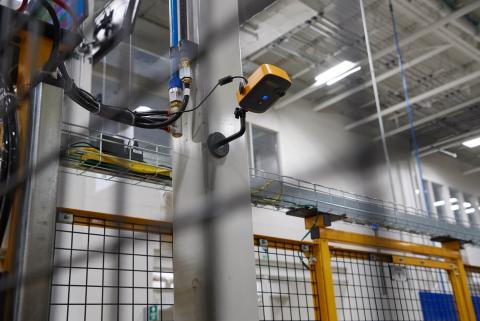
主动维护的好处是众所周知的,所以为什么不维护世界各地吗?障碍包括:
- 改变维护文化从“预防性”到“预测”是一个缓慢的过程。
- 全职资源分配学习和执行分析设置和培训需要大量投资。
- 维护团队需要一年多的训练,精通了解振动,这可以测试经理的决心。
- 通常,只有公司过程足够“关键”影响石化停机时间成本和安全等等问题,发电,纸浆和造纸行业实现状态监测。一些公司冗余系统代替振动监测,因为他们的资产的复杂性。
你想主动的维护并不是可行的为你的设备,你必须选择:
- 定期更换部件磨损
- 外包振动顾问
- 使用原始的技术分析机器的状态
- Run-to-fail(高成本,很难摆脱)
领导人可以通过两种方式方法积极的维护程序
理想化方法
专用的预见性维护(PdM)或在大型工业厂房可靠性团队的人,时间和预算去做积极主动的工作,确定厂内的最关键的设备。这样的团队将使用一个自动化的系统/机监控设备和存储和跟踪数据,决定当设备需要维护优化性能,防止损坏或失效。
我们其余的人
一个小型保养团队在一个中型工业或大型商业设施没有专门的人进行预测性维护他们可以管理,但最好的反应性实践。这样的团队将有广泛的责任,而不是范围或预算来证明完整SCADA或传感器远程监控。他们会手动收集数据的工作指令完成工作和解决问题,因为他们出现。
技术改进,维修技术人员可以使用相同的技术和工具来解决以及检查、日志和共享的基础主动维护。
五大趋势在工业维护
- 停机时间是越来越贵。设施的规模和商品成本增加设施越来越专业。
- 维护必须用较少的资源做更多的事。劳动力正变得更精简:专家退休但不会被取代。生产要求在预算不断减少。即时过程是减少犯错的余地。
- 意识正在迅速增长。维护最佳实践的价值产生了强大的行业影响力和专业协会的注意。可靠性是在董事会会议室讨论。维护不再仅仅是做生意的成本;这是一个卓越运营和战略优势的一部分。
- 新的维修技术正经历着大规模采用。价格正在下降,性能改善的工具。技术进步使复杂的工具更聪明和更容易使用所有technicians-not专家或专家。许多行业所看到的一个动态变化的理想混合外包和内部维护。
- 公司越来越多地使用维护最佳实践来巩固和扩展他们的竞争优势。实现维护最佳实践可以帮助公司实现结果如提高过程质量和降低运营成本(包括部分和合规支出少)。